Products
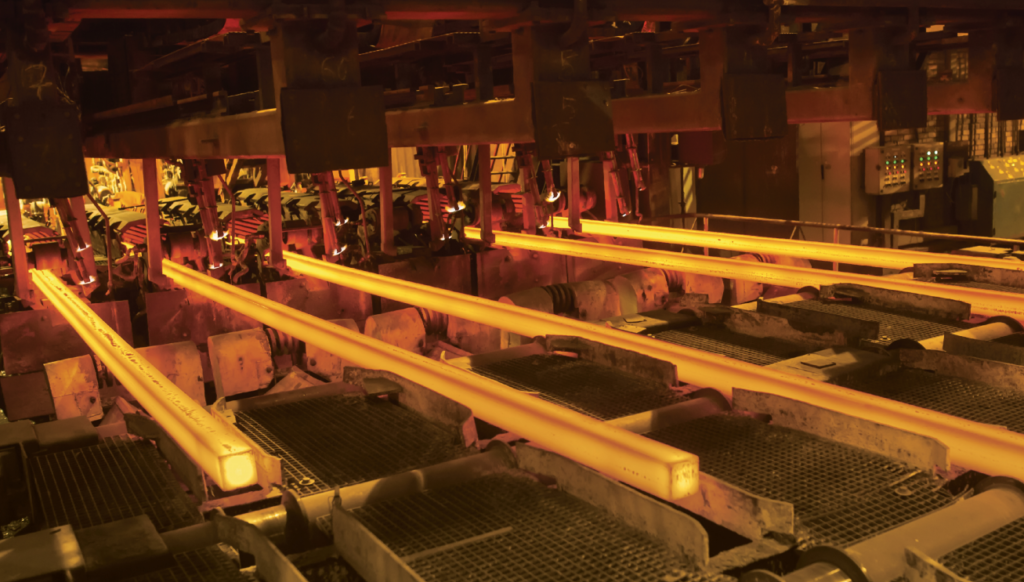
Product
BILLETS
Billets are intermediate steel products from which reinforcement bars are rolled. At At Steel, we produce our own billets to ensure consistent physical and mechanical properties in our rebars. We use premium quality raw materials to manufacture our bills, which are both corrosion-resistant and high in tensile strength. Our billets adhere to international standards, including ASTM A05, ASTM A706, and BS 4449 2016
We also manufacture steel bars tailored to custom-made orders, ensuring that each product meets the specifio requirements and preferences of our clients.
Products
Our Products

Supreme ( Astm A-615)
Minimum Yield Strength: 60,000 PSI (420 MPA)
Minimum Tensile Strength: 80000 PSI (550 MPA)
Bar Elongation: 8-10%

Flexible Elite ( Astm A-706)
Minimum Yield Strength: 60,000 PSI (420 MPA)
Maximum Yield Strength: 78000 PSI(540 MPA)
Minimum Tensile Strength: 80,000 PSI (550 MPA)
Tensile to Yield Strength Ratio > 1.25
Bar Elongation: 12-14%

Earthquake Resistance Re-Bar (BS4449_G500)
Minimum Yield Strength: 72,500 PSI (500 MPA)
Minimum Tensile Strength: 88,000 PSI (607 MPA)
Revised British Standard 2016
longation Minimum= 12.5%

Universal Testing
Machine (Utm) Lab
At UTM lab, we are dedicated to ensuring that every steel bar produced meets the most stringent standards of strength and durability. Through a series of rigorous tests and advanced precision analysis, we evaluate the material’s integrity at every stage of production. By identifying potential weaknesses and verifying compliance with industry benchmarks, we empower manufacturers to consistently deliver high-quality steel products that stand the test of time.
Our state-of-the-art equipment and expert technicians are at the forefront of innovation, ensuring that each bar is reliable, resilient, and fit for the toughest applications. With a steadfast commitment to excellence, UTM lab plays a crucial role in maintaining product integrity, giving clients the confidence to meet and exceed the demanding requirements of modern construction and engineering projects.
UTM lab is used to test tensile strength (pulling), compressive strength (pushing), flexural strength, bending, shear, hardness, and torsion, providing essential data for material design and quality materials.
Our Process
Scrap
We source high-quality scrap, including HMS1, HMS 1&2, and ISRI, from various regions worldwide, primarily Europe. Our facility is equipped with heavy-duty cranes for efficient scrap transfer. Industrial magnets are utilized to convey the scrap into our induction furnace for melting.
Electric Induction Furnace
Scrap is loaded into our furnace using industrial buckets, where it is melted and transformed into prime billets. Throughout this process, we meticulously monitor the chemical composition- including Carbon, Manganese, Phosphorus, Sulfur, and Silicon-to ensure the billets meet international standards.
CCM
Scrap melted in the induction furnace is processed through the Continuous Casting Machine, which precisely converts the molten material into billets for the steel-making process.
Billets
These precisely hot-rolled billets, the primary raw material for steel rebars, are now ready for direct rolling in the mill.
Rolling Mill
The hot-rolled billets are transported via conveyors to our automatic rolling mill, where they are transformed into steel rebars.
Cooling Bed
The hot steel rebars are transferred to our 120-foot cooling bed, where they are carefully cooled and precisely cut to length, either per foot or according to customer specifications, before being prepared for bundling.
Dispatch
Before dispatch, steel rebars are carefully weighed and bundled. To ensure compliance with international standards, random testing is conducted in our in-house laboratories, with any rejected pieces promptly separated. Each bundle is then labeled with our tag, signifying it is ready for dispatch.
OUR CLIENTS
We believe in gaining our
customers' trust.











